Back to GMA Membership Directory
Associate 1-100
Professional Bio
As an Operations Manager at Endeavor 3D I am responsible for Capital Project Management, Quality and Testing Laboratory capabilities, Logistics coordination, Additive Manufacturing technologies and process support. I also lead the Multi-Jet Fusion (MJF) Department Production Operations. Prior to my role as Operations Manager, I was an Applications Engineer at Endeavor3D as well. Diving deep in additive manufacturing capabilities and scalability.
Prior to joining the Jacobs Institute in 2020 as a Sr. 3D Printing Tech and Manufacturing Supervisor specializing in Digital Anatomy 3D Printing, I have also been heavily involved with additive manufacturing in my previous role as a Engineering Technician where I operated large scale DED, laser powder bed fusion, binder jetting, sintering, metallurgical analysis, and material characterization. I also gained experience with internal part inspection, learning and creating best practices for proper inspection processes for production parts through utilization of Coordinate Measuring Machines (CMMs), optical measurement like optical comparators, digital and dial micrometers and calipers, dial gauges, and thread gauges.
I have also worked in large and small scale machine shops where I specialized in writing programs, tool path generation, and multi-axis system set-ups including: Cincom CNC Swiss Lathes, DMG Mori and Mazak CNC Lathes, Hurco CNC Mills, and Soroluce Boring Mills specifically for Subtractive Manufacturing.
My professional project portfolio includes the America Makes MAMLS Feature-Based Qualification Method for Directed Energy Deposition Additive Manufacturing program and a series of projects for EWI’s Additive Manufacturing Consortium (AMC). HP Digital Manufacturing Partnership.
Anatomical model manufacturing located in the medical campus in downtown Buffalo, NY
Prior to joining the Jacobs Institute in 2020 as a Sr. 3D Printing Tech and Manufacturing Supervisor specializing in Digital Anatomy 3D Printing, I have also been heavily involved with additive manufacturing in my previous role as a Engineering Technician where I operated large scale DED, laser powder bed fusion, binder jetting, sintering, metallurgical analysis, and material characterization. I also gained experience with internal part inspection, learning and creating best practices for proper inspection processes for production parts through utilization of Coordinate Measuring Machines (CMMs), optical measurement like optical comparators, digital and dial micrometers and calipers, dial gauges, and thread gauges.
I have also worked in large and small scale machine shops where I specialized in writing programs, tool path generation, and multi-axis system set-ups including: Cincom CNC Swiss Lathes, DMG Mori and Mazak CNC Lathes, Hurco CNC Mills, and Soroluce Boring Mills specifically for Subtractive Manufacturing.
My professional project portfolio includes the America Makes MAMLS Feature-Based Qualification Method for Directed Energy Deposition Additive Manufacturing program and a series of projects for EWI’s Additive Manufacturing Consortium (AMC). HP Digital Manufacturing Partnership.
Anatomical model manufacturing located in the medical campus in downtown Buffalo, NY
Company
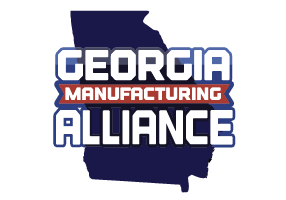